You’ve done everything right regarding 3PL inventory management and upped your re-orders; but despite your best efforts, you’re still selling through your stock. This is good news — you have a popular product that customers love. Either that, or it could be that there’s a problem with your warehouse management process.
So how do you ensure your warehouse operations are in top gear to keep your customers coming back? After all, you don’t want poor warehouse management to cause excessively delayed timelines and broken customer promises. This is where a warehouse management system (WMS) is critical.
What does backorder mean?
Put simply, businesses experience inventory backorders when the demand for a product exceeds available stock. On the one hand, as stated above, a backorder can be a sign of a product selling like hotcakes. On the other, backorders can also be a result of a few unfavorable factors, such as product delays, forecasting errors, shipping delays, etc.
For a product to be deemed a “backorder,” the out-of-stock product should be in production and available to restock inventory. In other words, if a product is out of stock but still available for purchase, it is a backorder.
The longer and more complicated the supply chain, the higher the negative impact on the supply chain. For starters, if backorders are not dealt with correctly, they can lead to reduced customer retention and loyalty. Apart from that, backorders can also lead to The Bullwhip Effect — an overcorrection in the supply chain that can lead to excess inventory and added costs.
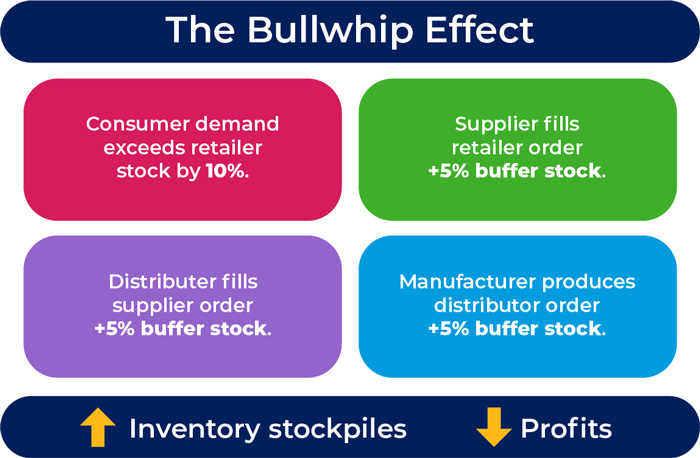
Now that we’re clear on the big question — what does backorder mean — it’s time we explore how a warehouse management system (WMS) can benefit your business.
Before we get there, you can also learn more about how WMS and OMS can drive customer-centric growth.
What is 3PL inventory management?
The 3PL in 3PL inventory management is short for third-party logistics. It describes when businesses outsource storage, transportation, and delivery to an outside logistics provider. 3PL providers manage inventory for businesses by storing their goods in their warehouses and ensuring timely delivery. They often use state-of-the-art warehouse management system software like Pivotree WMS for accurate inventory, streamlined operations, and reduced costs.
What are the benefits of using 3PL inventory management? When you use a 3PL provider, you can focus more on what your business does best — and less on logistics.
Here’s how to manage Backorder Fulfillment with a Warehouse Management System
- Real-time inventory visibility: A WMS provides accurate and real-time visibility of inventory levels. Warehouse management system software continuously updates inventory data as items are received, picked, or shipped. This visibility ensures that backordered items are closely monitored and allocated for fulfillment the moment they’re made available.
- Smart prioritization: A WMS can improve warehouse management operations by prioritizing backorders based on predefined rules and criteria — no human intervention, no time-consuming judgment calls. These rules can include customer priority, order date, shipping deadlines, or any other factor critical for business objectives. The system can automatically identify and prioritize critical backorders, ensuring that they are fulfilled promptly once stock is available.
- Order consolidation: With automation-driven warehouse operations, businesses can optimize order consolidation by grouping backorders by item type, geography, or other similarity parameters. This allows efficient picking and packing, making multiple backorders easier to handle.
- Automated picking and packing: Warehouse management systems can integrate with automation technologies such as conveyors, sortation systems, and robotic picking systems. This enables automated retrieval of backordered items from their storage locations and seamless integration into the packing process. Automated pick-and-pack also increases speed and accuracy, reducing fulfillment time and minimizing errors.
- Dynamic slotting: Automated warehouse management system software leverages historical data and order patterns to optimize order placement, or “slotting,” of backordered items to ensure that they are easily accessible. The impact, once again, is reduced picking time and improved productivity.
- Improved labor management: Labor is an integral part of the warehouse, and a WMS helps organizations make the most of their workforce. With real-time visibility of worker performance, a warehouse management system can help organizations balance workloads and assign picking tasks based on availability to dynamically adjust workforce allocation in a way that’s aligned with demand fluctuations.
- Handling exceptions: Warehouse operations and contingencies go hand in hand. When exceptions such as delayed shipments, inventory discrepancies, or incomplete orders crop up, a WMS can proactively detect these exceptions, raising alerts and notifications for the concerned teams to take immediate action and resolve the issue.
- Easy integration: WMS with integration capabilities helps align with external systems such as enterprise resource planning (ERP), customer relationship management (CRM), etc. This drives seamless communication and exchange of backorder statuses, customer information, and other data and eliminates manual efforts.
When you need a WMS that ticks all these boxes, Pivotree has you covered. Easy integration with existing monolithic systems, AI, and automation-driven excellence, 360-degree visibility of your warehouse operations — these are only a few of the many ways in which Pivotree WMS drives true warehouse excellence.
Got questions about Pivotree WMS? Speak to one of our supply chain experts today. Drop a line at [email protected].
Learn more about how to better deal with pre-orders and backorders.
About Pivotree: Pivotree designs, builds, and manages frictionless commerce experiences for brands and their customers around the world. We provide end-to-end solutions and services in Commerce, Data Management, and Supply Chain for hundreds of brands globally.
FAQs
1. How can businesses effectively manage backorders to prevent negative impacts on customer retention and loyalty, as well as avoid the Bullwhip Effect?
To effectively manage backorders and mitigate negative impacts on customer retention and loyalty, businesses need to implement strategies such as real-time inventory visibility, smart prioritization, and automated picking and packing. By closely monitoring backordered items and allocating them for fulfillment as soon as they become available, companies can ensure timely delivery and enhance customer satisfaction. Additionally, addressing the root causes of backorders, such as forecasting errors or shipping delays, is essential to prevent long-term disruptions in supply chain operations and minimize the risk of the Bullwhip Effect.
2. Besides prioritizing backorders and consolidating orders, how does a Warehouse Management System (WMS) address other challenges associated with managing backorders, such as inventory discrepancies or delayed shipments?
Apart from prioritizing and consolidating orders, a Warehouse Management System (WMS) tackles various challenges associated with managing backorders. For instance, WMS provides features like dynamic slotting to optimize the placement of backordered items for easy accessibility, automated picking and packing to enhance speed and accuracy, and improved labor management to balance workloads efficiently. Furthermore, WMS can handle exceptions such as delayed shipments or inventory discrepancies by proactively detecting issues and alerting the concerned teams for immediate resolution, thereby ensuring seamless warehouse operations.
3. While the benefits of using a 3PL provider for inventory management are highlighted, what specific challenges or considerations should businesses be aware of when outsourcing storage, transportation, and delivery to a third-party logistics provider?
While using a 3PL provider for inventory management offers benefits such as reduced logistics overhead and enhanced focus on core business activities, businesses should be aware of potential challenges. These may include limited control over inventory management processes, dependency on external providers for timely delivery, and the need for seamless integration with internal systems. Additionally, businesses should consider factors such as service level agreements, scalability, and data security when outsourcing storage, transportation, and delivery to a third-party logistics provider.